Bug-eye
lenses set up desktop chipmaking
By
Eric Smalley,
Technology Research News
The billion-dollar plants where computer
chips are made are a lot like the elaborate facilities where spaceships
are built. Imagine how cheap computers could be if chipmaking had more
in common with a process as simple as desktop publishing.
Researchers at Harvard University have taken a significant step in that
direction with the development of an array of microscopic lenses that
can shrink a pattern more than 1,000 times.
The microlens projection lithography technique uses ordinary white light
shining through overhead transparencies made with a desktop printer. Current
chipmaking processes involve ultraviolet lasers shining through tiny metal
masks that were etched by beams of electrons.
"The microlens array in our technique forms a ‘fly's eyes’ configuration
that images a common pattern and produces multiple, microscale [copies
of the pattern]," said Ming-Hsien Wu, a graduate student at Harvard University.
The lenses are modeled after the compound eyes of insects. Each of a fruit
fly's eyes, for example, is made up of about 800 separate lenses. Insects
use the many separate images compound eyes provide to help detect motion
or boost low-light vision.
Because the microlens process is limited to repetitive patterns, it's
not likely be used to make entire computer processors, but many other
chips and
sections of chips used in a wide range of electronic and optical devices
do have regular patterns. The technique could be used to produce transistor
arrays, storage devices, sensor arrays, pixel arrays, beam splitters,
optical gratings and color filters, said Wu.
Chips are ordinarily made by covering a layer of semiconductor with a
protective oxide layer, then a layer of photoresist, or plastic that reacts
to light. A mask outlining a pattern is positioned above the chip and
light is shone through the mask. The light alters the exposed areas of
the photoresist, allowing specific chemicals to wash it away along with
the oxide underneath. The remaining photoresist is washed away with other
chemicals, leaving the layer of oxide in the form of the mask and the
layer of semiconductor exposed in the original pattern. The exposed silicon
is then "doped," or altered, to become electrically conductive. Manufacturers
make chips with feature sizes as small as 180 nanometers using this process.
The microlens projection technique instead uses arrays of one of two types
of lenses: polystyrene microspheres or convex microlenses. The researchers
have produced uniform patterns on 2-square-centimeter surfaces by projecting
25-square-centimeter transparency images through arrays of microspheres
1.5 to 10 microns in diameter, said Wu.
Chips made using microspheres had chip features as small as 200 nanometers,
while the similar microlense technique allowed for features as small as
400 nanometers.
Current chipmaking processes include steps that reduce pattern sizes four
or five times, said Wu. The small scale of the masks and light sources
used to do this make these processes sensitive, which is is one reason
they are expensive. "In conventional lithography, the formation of patterns
on photoresist is very sensitive to the lateral and vertical positions
of the chromium masks and it requires high-precision stages to control
the positions of the masks," said Wu. "The whole lithographic facility
has to be placed in an environment with very low background vibration."
"In our technique, the formation of patterns on photoresist is much less
sensitive to the positions of the transparency masks," said Wu. "For a
25-by-25-square-centimeter transparency mask, even a one centimeter shifting
of the mask would not cause obvious change in the shape of the produced
patterns," he said.
The microlens photolithography technique could be used in practical applications
in two to five years, said Wu.
Wu's research colleague was George M. Whitesides. They published the research
in the April 16, 2001 issue of the journal Applied Physics Letters. The
research was funded by the Defense Advanced Research Projects Agency (DARPA).
Timeline: 2-5 years
Funding: Government
TRN Categories: Integrated Circuits
Story Type: News
Related Elements: Technical paper, "Fabrication of arrays
of two-dimensional micropatterns using microspheres as lenses for projection
photolithography," Applied Physics Letters, April 16, 2001
Advertisements:
|
June
6, 2001
Page
One
Search scheme treads
lightly
Bug-eye lenses
set up desktop chipmaking
DNA parts make
versatile nanotubes
Watermarks hide in plain
text
Material bends sound waves
News:
Research News Roundup
Research Watch blog
Features:
View from the High Ground Q&A
How It Works
RSS Feeds:
News | Blog
| Books 
Ad links:
Buy an ad link
Advertisements:
|
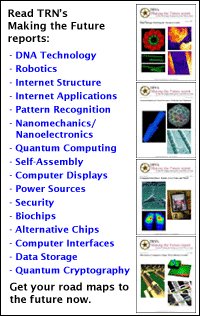
|
|
|