Plastic
mix promises big displays
By
Eric Smalley,
Technology Research News
Big city newcomers can be overwhelmed by
a blur of shapes and colors as buses, trolleys and delivery trucks wrapped
in photo-quality advertising images whiz by. Imagine how much more disorienting
the experience would be if the vehicles sported giant video displays.
There's a long way to go from today's flatscreen technology to something
that can be painted on a large surface, but researchers at Philips Research
Laboratories and Eindhoven University of Technology in the Netherlands
have taken a big step in that direction.
Liquid crystal displays (LCDs) are usually made by sandwiching liquid
crystals between two carefully positioned sheets of glass. Liquid crystals
are long, randomly arranged molecules that line up in crystal-like order
in the presence of an electric field. The molecules reflect light differently
when they are ordered and disordered, which allows them to form pixels
in a display.
The researchers have come up with a method for layering liquid crystals
on a single surface of glass, plastic or silicon.
Because there's only one substrate rather than a sandwich of two, the
displays can be very thin. "The single-substrate technology reduces the
thickness of the display [to] smaller than 0.5 millimeters," said Dirk
Broer, a research fellow at Philips Research Laboratories and a professor
of polymer chemistry at Eindhoven University of Technology.
The process could lead to displays that are larger, thinner and more flexible
than today's screens, said Broer. "It opens ways to make portable equipment
smaller, [lighter] and more robust," and to make displays large enough
to cover walls, he said.
To make the single-substrate screen, the researchers spread a liquid blend
of plastic and liquid crystals onto a surface containing a grid of electrodes.
The electrodes produce the electric field necessary to power individual
pixels. The researchers then used two types of ultraviolet light to harden
the plastic in the blend, forming a covering to contain the liquid crystals.
The researchers formed plastic walls on the substrate by shining 400-nanometer
wavelength light in a grid pattern. Then, to form a top coat of plastic,
they shined 340-nanometer light on the whole assembly. The end result
was a grid of 500- by 500- by 10-micron boxes that contained the liquid
crystal. Five hundred microns is about the diameter of a period-size dot.
The grid walls were 100 microns thick and the cover layer 10 microns thick.
The researchers' prototype display takes 5 to 40 thousandths of a second
to switch a pixel on and off and produces images with a contrast ratio
of 1 to 20, according to Broer. Typical commercial LCDs have comparable
switching times that range from 10 to 200 milliseconds, but better contrast
ratios of at least 1 to 200, which result in clearer images and more vibrant
colors.
The researchers' next steps are to improve the contrast ratio and brightness
of the display and develop pilot production lines, said Broer. They are
also working on using substrates with thin film transistors in order to
use active matrix addressing, he said. Active matrix addressing systems
are faster, enabling displays to show video.
The process could be used to make simple displays in two to five years,
said Broer. The LCD process might never come to market if an alternative
technology, organic light emitting diodes (OLEDs), matures sooner, he
said. OLEDs could lead to displays made entirely out of sheets of plastic.
Broer's research colleagues were Roel Penterman, Stephen I. Klink, Henk
de Koning and Giovanni Nisato of Philips Research Laboratories. They published
the research in the May 2, 2002 issue of the journal Nature. The research
was funded by Royal Philips Electronics.
Timeline: 2-5 years
Funding: Corporate
TRN Categories: Materials Science and Engineering
Story Type: News
Related Elements: Technical paper, "Single-substrate liquid-crystal
displays by photo-enforced stratification," Nature, May 2, 2002
Advertisements:
|
May
15/22, 2002
Page
One
Viruses turn out high-tech
materials
Virtual touch controls
rats
Laser bridges
infrared-microwave gap
Plastic mix promises
big displays
Laser patterns particles
in 3D
News:
Research News Roundup
Research Watch blog
Features:
View from the High Ground Q&A
How It Works
RSS Feeds:
News | Blog
| Books 
Ad links:
Buy an ad link
Advertisements:
|
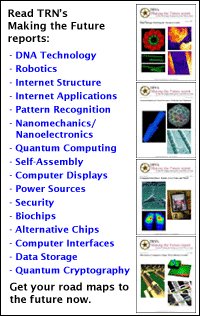
|
|
|