Biochips
get pumped
By
Kimberly Patch,
Technology Research News
An important aspect of making microscopic
machines is producing minuscule versions of basic mechanical parts like
pumps that can shunt around tiny amounts of matter.
Scientists from the Colorado School of Mines have constructed two types
of valves and two types of pumps that are not much bigger than a red blood
cell. "We have the ability to locally control minute volumes of fluid
as well as individual particles or cells in microsystems," said John Oakey,
a Colorado School of Mines researcher.
The devices, which are an order of magnitude smaller than existing micro
pumps, are a step toward making microscopic biological and chemical labs-on-a-chip,
including sensors or drug delivery vehicles that could be implanted within
human bodies.
The pumps are twice the size of red blood cells and push forward one millionth
of a liter, or about one 20th of the volume of a drop of water, per hour.
The key to the microscopic mechanics is positioning groups of spherical
particles within tiny channels and using them to coax liquid to flow in
a particular direction, said Oakey. The insight that led to the devices
was realizing that colloidal spheres could be used as the active parts,
he said.
A colloid is a liquid mixture that contains particles finer than those
generally suspended in a solution.
These colloidal building blocks measure three microns across, and the
mechanical devices just under 10 microns, or one hundredth of a millimeter.
A red blood cell is about five microns in diameter.
To make the parts, the researchers corralled the colloids they needed
from the solution and positioned them using laser tweezers. Laser tweezers
are computer-controlled laser beams that bombard the minute particles
with photons in order to manipulate them in a way similar to the way a
strong wind can move solid objects. The pumps "operate by controlling
the motion of a few individual colloidal particles that comprise the pieces
of the pump," said Oakey.
To make a valve the researchers used laser tweezers to line up a group
of colloids as they floated within the tiny channel, then polymerized,
or cemented the particles together to form the flap of the valve. "In
a focused laser beam, multiple particles will align... with the beam,"
said Oakey. "The interaction of the trapped particles and the surrounding
hydrogel [solution] results in the polymerization," he said.
The researchers two pump designs -- gear and sine-wave -- operate on the
same principles as their macroscopic cousins, said Oakey.
Gear pumps are generally made of a pair of gears that trap fluid against
the walls of a chamber. The trapped fluid causes a drop in pressure across
the gears and the meshing of the gears in the center prevents fluid from
falling back through the gears.
Although the round particles and straight-walled channels don't fit as
precisely as precision-machined gears, the basic effect is the same, said
Oakey. "The particles in our pump are always in contact in the center...
like meshing gears, [and] around the outer perimeter the particles are
almost contacting the walls. These gaps around the perimeter trap fluid
and [push] it forward incrementally."
A screw, or sine-wave pump works in a similar way. As the screw mechanism
turms, a plug of fluid is trapped, propelled along with the threads, and
spit out the other side. The sine-wave version works the same way, "except
in two dimensions and with much smaller plugs of fluid," said Oakey.
The researchers have also constructed two types of valves: a passive check
valve, which allows fluid to flow in only one direction, and a similar
valve that is moved around and opened and closed using laser tweezers.
"These valves... are simply a string of particles polymerized together
in situ, connected to a larger particle which serves as a tether," said
Oakey. The tether particle can either be attached to the wall of a channel
or held in place using laser tweezers.
The researchers thought of using colloidal particles to construct tiny
mechanical parts while using a particular set of laser tweezers they had
constructed as a tool to study the behavior of individual colloidal particles.
"We constructed an optical trap capable of rapidly manipulating individual
particles," Oakey said. Doing so "led us to recognize the potential utility
of incorporating individual colloidal particles within microchannels,"
he said.
The researchers' prototype pumps are already about an order of magnitude
smaller than existing devices, said Oakey. And in theory, colloidal pumps
could be made considerably smaller, said Oakey. "They could potentially
be scaled down by at least an order of magnitude," he said.
Aside from the colloidal pumps, "the smallest pumps I know of [move an
elastic] membrane using pneumatic actuation," said Oakey. These have reached
a size limit due to the dimensions of the membrane, he said. At a certain
point the membrane itself "prevents deflection into channels which are
too narrow -- the aspect ratios just get prohibitive."
What may eventually prove a size limitation for colloidal pumps is the
wavelength of light used by the optical tweezers, said Oakey. The colloidal
pumps "can theoretically be made... down to the diffraction limit of the
optical trap, and perhaps smaller," he said.
The researchers intend next to combine several of their microscopic devices
into a working array, said Oakey. Operating many pumps in parallel would
increase the amount of liquid the device could pump per hour, said Oakey.
The main goal of making a very small pump, however, is to accurately control
a very small amount of liquid, he said.
Many tiny pumps could eventually be included in more complicated systems
like quickly-acting biological assays or chemical sensors that could be
used within living bodies, said Oakey. "We are interested in [combining]
device arrays with sensing and feedback operations," he said. "Colloid-based
pumps and valves... could be incorporated within implantable devices in
vivo and used as monitoring or targeted drug delivery vehicles," he said.
Oakey's research colleagues were Alex Terray and David W. M. Marr. They
published the research in the June 7, 2002 issue of the journal Science.
The research was funded by the National Science Foundation (NSF) and the
National Aeronautics and Space Administration (NASA).
Timeline: 2-5 years
Funding: Government
TRN Categories: Microfluidics and BioMEMS
Story Type: News
Related Elements: Technical paper, "Microfluidic Control
Using Colloidal Devices," Science, June 7, 2002.
Advertisements:
|
August
21/28, 2002
Page
One
Biochips get pumped
Chip design aims
for quantum leap
Net traffic mimics
earthquakes
Stamps and glue make
circuits
Shortcuts lighten
wireless load
News:
Research News Roundup
Research Watch blog
Features:
View from the High Ground Q&A
How It Works
RSS Feeds:
News | Blog
| Books 
Ad links:
Buy an ad link
Advertisements:
|
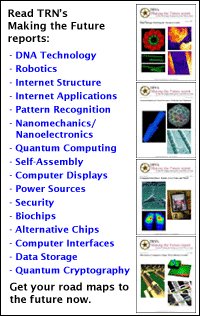
|
|
|