Microwave
drill melts concrete
By
Eric Smalley,
Technology Research News
Cross a microwave oven with a nail and
you get a drill that makes holes by melting the material in its path.
Researchers at Tel Aviv University in Israel have made a prototype microwave
drill that can make a 2-millimeter-diameter, 2-centimeter-deep hole in
concrete in about a minute.
The microwave drill is quiet, doesn't produce dust, and is less expensive
to make than laser drills, said Eli Jerby, an associate professor of physical
electronics at Tel Aviv University in Israel. Once the drill is optimized,
it should work as fast as mechanical drills, he said. The principal behind
the drill can be used to make other tools as well, he said.
The drill works on materials like ceramics, concrete and glass, which
tend to absorb microwaves, but doesn't work on conductors like metals,
which reflect microwaves, said Jerby. It could be used in production lines
in the electronics, automobile, ceramics, glass and construction industries,
and for geological applications, he said.
The drill bit serves as an antenna to focus microwave energy on a small
spot under the surface of the material, and the intense microwave energy
rapidly melts the material in this spot, said Jerby. Instead of spreading
microwave energy over the entire chamber of a microwave oven, "we... compress
the energy into a much smaller volume -- less than 1 cubic centimeter,"
said Jerby. The temperature within the small spot rapidly exceeds 1,500
degrees Celsius, which is hot enough to melt many materials.
This heating happens rapidly because of the thermal runaway effect, Jerby
said. The effect begins when the focused microwaves, which are 122 millimeters
long, produce a 1-millimeter hot spot. The intense heat modifies the properties
of the material in the hot spot so that it absorbs the microwaves even
more readily. This "further localizes the heating in an exponential growth,
leading to an extremely high temperature in a small spot," said Jerby.
Once a hot spot is created, the microwave drill pushes into the softened
material, and moves the hot spot forward, said Jerby. The bit moves through
the material like a hot knife going through butter, he said.
The concept that led to the drill was the idea to produce a localized
thermal runaway effect on purpose, said Jerby. The thermal runaway effect
is usually undesirable, he said.
Useful applications of the effect are not limited to drilling, said Jerby.
"Derivatives of the microwave drill could be used for cutting, nailing,
jointing or just for local heating," he said. The researchers have used
the drill to insert metal pins into hard materials, for example, said
Jerby. "One can use the microwave drill to replace three successive operations
-- drilling, nailing and gluing." Nailing is accomplished by leaving the
bit in the material, and when the softened material cools and hardens,
it glues the nail in place.
The main disadvantages of the device are that it could be a radiation
hazard and it can produce heat stress effects like cracks, said Jerby.
These make the drill appropriate only for professional workers and automatic
production lines and not for do-it-yourselfers, he said.
Under normal operations, the radiation hazard posed by the drill is comparable
to that of a microwave oven, Jerby added. "We [have] reached this safety
level in our lab," he said.
The cost of a drill made from microwave oven components is comparable
to the cost of a mechanical drill, said Jerby. However, it's more likely
that commercially available microwave drills will be more expensive versions
tailored for specific applications, he said.
The researchers' prototype is about 30 centimeters tall. Inside the drill
is a 5 to 30 millimeter diameter cylinder encompassing the drill bit.
The bits range from 0.3 to 6 millimeters in diameter.
The idea of the microwave drill appears sound and is relatively novel,
said James R. Thomas, a professor of mechanical engineering at Virginia
Polytechnic Institute. There are niche applications where it could be
competitive with other types of drills, said Thomas. However, "it would
be limited to relatively small holes and it will not be as precise as
a laser drill," he said.
The researchers next steps are working on ways to prevent the drill from
inducing thermal stress effects like cracks, dealing with safety issues,
adapting the drill to make larger and smaller holes, studying materials-related
effects produced by the drill, and developing derivative devices, said
Jerby.
The microwave drill could be used in practical applications today, said
Jerby. "We have working prototypes for ceramic materials, concrete and
glasses," he said. "These can be industrialized within one to two years."
Jerby's research colleagues were Vladimir Dikhtyar, Oleg Actushev, and
Uri Grosglick. They published the research in the October 18, 2002 issue
of the journal Science. The research was funded by Tel Aviv University.
Timeline: Now
Funding: University
TRN Categories: Materials Science and Engineering
Story Type: News
Related Elements: Technical paper, "The Microwave Drill,"
Science, October 18, 2002
Advertisements:
|
October
30/November 6, 2002
Page
One
Nanoscale LED debuts
Data transfer demo
sets speed mark
Pulling nanotubes makes
thread
Text software spots
intruders
Microwave drill melts
concrete
News:
Research News Roundup
Research Watch blog
Features:
View from the High Ground Q&A
How It Works
RSS Feeds:
News | Blog
| Books 
Ad links:
Buy an ad link
Advertisements:
|
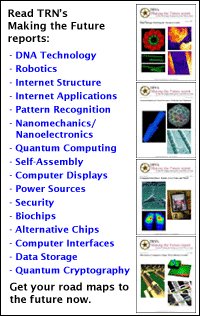
|
|
|