Plastic transistors go vertical
By
Kimberly Patch,
Technology Research News
Silicon transistors have proven to be extraordinarily
useful -- they are the nerve cells in the brains of desktop computers,
laptops, handhelds and the computers embedded in everything from cars
to watches.
But even though electronics have steadily grown cheaper, most
researchers agree that it would be difficult to get the cost of even a
simple silicon chip below 75 or 50 cents due to the cost of manufacturing
silicon, which involves cleanrooms and etching processes.
At the same time, there are clear markets for cheaper electronics.
Put a computer chip on every item in the grocery store, and checkout and
inventory would become fast and automatic.
Inexpensive transistors can be made by printing organic polymer,
or plastic, onto a surface with an inkjet printer rather than etching
the devices into silicon, but today's plastic transistors are relatively
large and therefore inefficient.
Researchers from the University of Cambridge in England have brought
inexpensive, practical organic transistors a step closer to your grocery
cart by devising a pair of processes that form small, vertical transistors
from layers of printed polymer.
The processes could be used to print low-cost electronics onto
flexible surfaces like plastic, leading to electronic tags that cost less
than five cents, said Henning Sirringhaus, a reader in physics at the
University of Cambridge. It could also enable very large active matrix
display screens, he said. "If you can make electronics cheaply over large
areas then you can do things that are not possible today," he said.
A transistor consists of source and drain electrodes that carry
current into and out of a channel, and a control electrode that regulates
the flow of current to turn the device on and off.
The trick to making small, efficient transistors is defining a
clear channel between the source and drain electrodes. The smaller the
channel, the more efficient the transistor.
One way to do this is to make the transistors vertically by stacking
three layers of materials: an insulator, or channel, layer sandwiched
between source and drain electrode layers. Using this method, the researchers
were able to define a channel length as small as 0.7 microns, which is
a little less than the diameter of an E. Coli bacteria. The transistor
channel length in a Pentium 4 chip is around 0.1 microns.
Using the layering method, however, requires that layered materials
be cut into individual transistors and a control electrode be added to
each transistor.
Silicon transistors can be made this way by etching the layers
with a beam of ions, but etching does not work well with polymers. Polymers
break down under etching conditions, and layers of different types of
polymer are etched away at different rates, yielding a corrugated surface
rather than the requisite smooth sidewall, said Sirringhaus.
The researchers discovered that they could separate organic transistors
by pressing a wedge into the polymer layers so that the layers were pressed
apart sideways rather than smeared downwards, said Sirringhaus. "I compare
this to... black forest tarts -- they have layers of chocolate, layers
of cream and layers of cherry. What we were trying to do is cut a black
forest tart without getting cherries into the chocolate [in order to]
maintain the integrity of that multilayer structure," he said.
The researchers first used the method to cut a transistor channel
in a single layer of polymer to make a horizontal organic transistor.
It worked well enough that they attempted to use the method with several
layers, Sirringhaus said. "The surprise was that we got that relatively
crude... approach to give such beautiful, well-defined vertical sidewalls,"
he said.
The process could eventually be used with even more complex multilayer
structures, said Sirringhaus.
The method is compatible with the printing process, said Sirringhaus.
"All you need to do is use printing to define the coarse features of the
electrodes, and then use the embossing step to define submicron [gaps]
and it's all compatible with competitive manufacturing techniques," he
said.
For the vertical transistors to be practical, however, the researchers
needed a way to add control electrodes that are the proper size. Oversize
control electrodes slow down the electronics. The researchers used the
vertical transistor method to make prototype transistors with 5-micron
channel lengths, but they could not use the printing process to add a
feature less than sixty microns in size because there's a minimum size
droplet the printer can handle. "That is a large overlap. Ideally, if
you have a 5- micron channel you would also like to have a 5- or 6- or
7-micron-wide gate electrode," Sirringhaus said.
The researchers solved the problem by taking advantage of a groove
that is an artifact of the cutting method, said Sirringhaus. "The location
of the topographic groove -- that's where the channel is," he said. "The
groove can be very narrow, so you can print a large inkjet droplet and
all the ink is sucked into that narrow groove. That's a way of self-aligning
the gate electrode."
The small channel length and the small, well-aligned gate electrode
could produce circuits that are nearly two orders of magnitude faster
than existing organic circuits, said Sirringhaus. The researchers have
not yet tested the transistors in circuits.
The researchers have found a creative way to fabricate a short
transistor channel, and the method is an advance in one step of device
fabrication, said Sigurd Wagner, a professor of electrical engineering
at Princeton University. The technique is novel because it combines two
innovations, Wagner said. "It uses embossing, which in turn is enabled
by employing a plastic substrate," he said.
The method is imaginative, and is a step forward in finding ways
to produce high-resolution plastic circuits for flexible displays and
other systems, said John Rogers, a researcher at Lucent Technologies Bell
Labs. "This nano cutting approach, together with... stamping, molding
and imprinting techniques that have been previously demonstrated, constitute
a... toolkit of methods for building plastic electronic circuits," he
said.
This type of work could yield flexible paper-like displays, and
ultra low-cost sensors and ID tags "that have the potential to revolutionize
the way that we think about consumer electronics," said Rogers.
The next step in commercializing the technology is testing how
manufacturable the technique is, said Sirringhaus. This will fall to Cambridge
startup company Plastic Logic, formed to commercialize the inkjet printing
of transistor technology, Sirringhaus said. "We will need to see how well
the technique compares in terms of manufacturing, yields, reliability
-- those are all things that we don't do at the University," he said.
The method could be used to produce inexpensive plastic electronics
in two to five years, according to Sirringhaus.
Sirringhaus's research colleagues were Natalie Stutzman and Richard
H. Friend. The work appeared in the March 21, 2003 issue of Science. The
research was funded by the Swiss National Science Foundation and Cambridge
University.
Timeline: 2-5 years
Funding: Government, University
TRN Categories: Integrated Circuits; Materials Science and
Engineering
Story Type: News
Related Elements: Technical paper, "Self-Aligned, Vertical-Channel
Polymer Field-Effect Transistors," Science, March 21, 2003.
Advertisements:
|
June 4/11, 2003
Page
One
Shock waves tune light
Artful displays track data
Plastic transistors
go vertical
Artificial
beings evolve realistically
News briefs:
Microfluidics go
nonlinear
Browser boosts
brain interface
Semiconductor
emits telecom light
3D display widens view
Study shows
DNA will fill tubes
DNA part makes transistor
News:
Research News Roundup
Research Watch blog
Features:
View from the High Ground Q&A
How It Works
RSS Feeds:
News | Blog
| Books 
Ad links:
Buy an ad link
Advertisements:
|
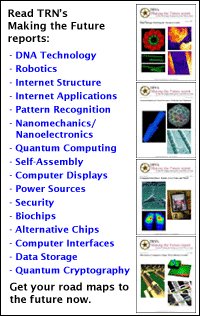
|
|
|