Segway robot opens doors
By
Eric Smalley and Kimberly Patch,
Technology Research News
Researchers from Massachusetts Institute
of Technology have crossed a robotic arm with the bottom half of a Segway
to make a robot named Cardea that can traverse hallways and open doors.
Cardea, named after the Roman goddess of thresholds and door pivots,
is the one-armed first prototype of a robot designed to have three arms
and the ability to safely interact with humans at eye level.
The Segway scooter platform, with its dynamic balancing abilities,
makes the arm practical, said Una-May O'Reilly, an MIT research scientist.
"The Segway is... like an inverted pendulum," she said. "Regardless of
where the weight is on top of it... the platform is able to move with
balance."
This is important because when the robot arm moves, its center
of mass shifts. Without dynamic balancing, a robot that has arms and stands
as tall as a human would require a much larger base, said O'Reilly.
Cardea stands about five feet tall and weighs about 200 pounds.
It consists of the Segway base, sonar sensors that help in navigation,
a pair of cameras that form a rudimentary vision system, and a single
arm capable of five degrees of freedom -- two at the shoulder, one at
the elbow, and two at the wrist. It also has a kickstand in the form of
spring-loaded legs that deploy when the robot is in danger of falling,
usually due to low battery power.
The prototype is capable of navigating a hall, finding a door
and pushing it open, according to O'Reilly. This demonstrates "that we
have some of the pieces toward the issues and the challenges of mobile
manipulation," she said.
The idea behind building a mobile robot that stands as tall as
a human is to explore the ways a humanoid robot can interact with the
world, and to make sure it interacts safely, said O'Reilly. The researchers
are aiming to give the robot the abilities to recognize whether it's in
a room or hallway, recognize and manipulate objects, take instructions,
and learn. Given the ability to move around, Cardea can actively explore,
she said.
Traditionally, robotic arms have been used to manipulate parts
for manufacturing, but factory manipulators operate under a different
set of assumptions and within a different realm, said O'Reilly. The environment
must be structured in a way that allows them to anticipate, she said.
"Parts have to be arranged perfectly so that the robotic arm can interact
with them repetitively."
Moving a robotic arm outside a factory setting means teaching
the robot to deal with an environment that is not necessarily structured
in an organized fashion, said O'Reilly. The present incarnation of Cardea
performs a level of mobile manipulation in an unstructured environment,
she said. The challenge is making it both safe and able to deal with all
the clutter of the real world, she added.
The researchers are aiming to augment the sonar sensors on Cardea's
base with a heat-sensing system and improve its vision system with better
panning ability and arm-vision system coordination, said O'Reilly. They
are also planning to add a robotic hand to the arm, increase the number
of arms to three, and give the robot a head, said O'Reilly.
The researchers used a type of robot arm previously designed for
MIT's robot Cog. The arm was designed with safety in mind. Robotic manipulators
tend not to be sensitive to objects or people, and so are in danger of
hurting people or burning out their own motors when they meet an obstruction.
The arm contains a series elastic actuator system that, like biological
muscle, provides a buffer between the actuator force and the load it is
acting on. An embedded spring system senses forces interacting with the
arm. The spring provides feedback about the load and also allows the actuator's
motor to gradually apply the force needed to move the load. "We can actually
use the spring model to control the arms, and the arms become much safer
when they interact with things," said O'Reilly.
The researchers's plans for improving Cardea's arms call for adding
two more and also giving the robot a third degree of freedom at each shoulder
so that each arm has six degrees of freedom. The three arms will be of
different lengths, and will have different end effectors, or hands, designed
for different purposes. "You can imagine having different instruments
at the ends of the arms, and with that we get more flexibility in terms
of what the mechanical system can actually do when it has to interact
with the world," said O'Reilly.
The current prototype has a simple knob for pushing open doors.
The researchers are working on a hand that has three force-controlled
fingers. Other hand possibilities include pincers, grippers, flippers
and paddles.
The odd number of arms will also widen the robot's interaction
abilities, said O'Reilly. "When you've got three arms you can carry something
with two and then perform an operation on that object with the third,"
she said. And while two arms make a single pair, three arms can form three
different pairs, she added.
Once Cardea gains a full complement of arms, the researchers will
add a more sophisticated vision system that coordinates with the arms,
said O'Reilly. "We want to try and understand the various vision-based
manipulation problems and how to address them," she said.
Cardea will eventually gain a robotic head similar to the MIT
robots Cog and Kizmet, said O'Reilly. "Then we can have a robot that moves
around and has to deal with social interaction issues of human-to-robot
at human-height level," she said. Cog is a stationary humanoid robot that
consists of a head, arms and torso. Kismet is a stationary humanoid robotic
head that is capable of facial expressions.
The researchers are also aiming to use Cardea to explore more
general notions of behavior, said O'Reilly. The robot will, like its predecessors,
learn by exploring its environment and manipulating objects, and interact
with humans through facial expressions and tones of voice.
There's also the question of what social character an assistive
robot should have, said O'Reilly. "If we were to have a robot [wondering]
around the halls and available for assistance... what should the face
look like, [and] how should the robot negotiate its interactions, take
instructions and show that it's learned or is following them?"
The researchers are also looking at the issue of maintaining a
robot that would never really have to power down, O'Reilly said. This
would require that the robot understand when it is in need of energy and,
for instance, plug itself into the wall, she said. Not having to turn
off would be an advantage because complicated robots tend to have time-consuming
startup procedures.
MIT's Cardea project is one of a dozen projects at universities
and government labs around the country that involve building robots on
Segway bases. The projects were initiated under the Defense Advanced Research
Projects Agency (DARPA) Mobile Autonomous Robot Software (MARS) program.
The MIT robot and a similar NASA project "make a
strong case for the marriage of mobility and manual skill," said
Rod Grupen, an associate professor of computer science at the University
of Massachusetts, Amherst. Grupen and colleagues are also developing a
Segway-based robot under the DARPA program. "These projects... are
among the very first to achieve a robot that interacts with people in
a human scale environment," he said.
O'Reilly's research colleagues are Rodney Brooks, Paul Fitzpatrick,
Lijin Aryananda, Jessica Banks, Aaron Edsinger, Eduardo Torres-Jara, Paulina
Varchavskaya, Alana Laferty, Alex Moore, Jeff Weber, Charlie Kemp and
Kathleen Richardson. The research is funded by DARPA and by a corporation.
Timeline: Unknown
Funding: Corporate; Government
TRN Categories: Robotics; Human-Computer Interaction; Engineering
Story Type: News
Related Elements: Cardea Web site: www.ai.mit.edu/projects/cardea/
Advertisements:
|
November 19/26, 2003
Page
One
Segway robot opens doors
Jolts turn liquid to solid
Switch promises optical
chips
Physics tackles
processor problem
Briefs:
Molecular memory
is electric
Liquid crystal tunes
fiber
Nanotubes fortify
plastic film
Plastic display
circuit shines
Model leverages
nano tethers
Stamp forms organic
laser
News:
Research News Roundup
Research Watch blog
Features:
View from the High Ground Q&A
How It Works
RSS Feeds:
News | Blog
| Books 
Ad links:
Buy an ad link
Advertisements:
|
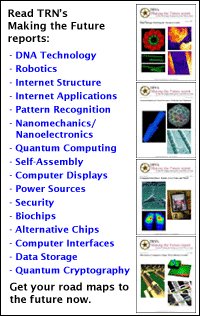
|
|
|