Pressure shapes plastic
By
Kimberly Patch,
Technology Research News
Today's recycling methods heat plastic to make it flow so it can be reshaped under pressure. The heating part of the process takes a toll, however, degrading the material and limiting the number of times it can be recycled.
Researchers from the Massachusetts Institute of Technology have made a plastic that can be reshaped using just pressure. The new plastic can be processed repeatedly without degradation, and the processing requires less energy than traditional plastic recycling methods.
The ability to shape plastic at low temperatures also makes it possible to mix thermally sensitive materials like biologically-derived pharmaceuticals with the material.
Key to the room-temperature reshaping is that the material, dubbed baroplastic, contains regions of two different plastics, one rigid, and one soft. These regions measure less than 100 nanometers, which is one tenth the diameter of an E. coli bacterium.
Under about 5,000 pounds of pressure per square inch, the plastic flows, even at temperatures as low as 25 degrees Celsius. "When placed under pressure, the rigid plastic starts to dissolve into the soft region, creating a mixture that can flow, like a slurry of ice and water, [and] can be molded into an object," said Anne Mayes, a professor of materials science and engineering at MIT. "When the pressure is released, the plastic rehardens," she said.
The difficult part was finding a mix of plastics with the right properties, said Mayes. "To find such systems, we first had to develop a new model to predict the behavior of polymer mixtures more accurately than previous models," she said.
The researchers were aiming to find a way to process plastics without the use of heat, but thought that it would be even more difficult to carry off. "When we first imagined processing plastics at room temperature, we thought we would need to have the rigid plastic completely dissolve into the soft plastic to get the material to flow," said Mayes. "Instead, we found that the systems can be molded in a semi-solid-state," she said. "It makes the concept much more versatile and potentially useful."
The concept fits well with current plastics recycling methods, because those processes already use pressure, said Mayes.
Baroplastics may have potential advantages beyond energy savings and high recyclability, said Mayes. "These materials might be excellent matrix materials for components that are thermally sensitive, such as biologically-derived pharmaceuticals [that] therefore cannot be incorporated into current thermoplastics," she said.
Designing a polymer so that pressure alone is enough to make it act like a fluid is "not only frightfully clever, but has the possibility of making a huge impact on the industry," said Galen Pickett, an associate professor of physics and astronomy at California State University of Long Beach.
With two carefully-chosen, carefully arranged components, and guided by a theoretical understanding of how compressing a mixture of polymers affects their mixing, the researchers "have built a new material with extremely useful properties," said Pickett.
The new material is just scratching the surface of what can ultimately be accomplished along these lines, said Pickett. "It makes one wonder what is possible when you have 20 or so plastics components to choose from, and have the freedom to arrange them with precision onto a linear chain," he said. "Every protein in a living organism is based on just such an arrangement, he added.
The researchers are working to develop new baroplastics combinations, said Mayes. They are currently experimenting with adding inorganic fillers to make materials with a wider range of mechanical properties, she said.
The first generation of the material could be technically ready for commercial applications in a few years, according to Mayes. Introducing a new plastic into the market is generally a difficult proposition, however, due to the low-cost, high-volume nature of the business, she added.
Mayes's research colleagues were Juan A. Gonzalez-Leon, Metin
H. Acar, Sang-Woog Ryu, and Anne-Valérie G. Ruzette. The work appeared
in the November 27, 2003 issue of Nature. The research was funded
by the Lord Foundation, Lord Corporation, the Seaver Institute, the National
Science Foundation (NSF) and the Office of Naval Research (ONR).
Timeline: 2-4 years
Funding: Corporate; Government; Institute
TRN Categories: Materials Science and Engineering
Story Type: News
Related Elements: Technical paper, "Low-temperature Processing of 'Baroplastics' By Pressure-Induced Flow," Nature, November 27, 2003
Advertisements:
|
January 14/21, 2004
Page
One
Quantum dice debut
Pressure shapes plastic
Software repairs
itself on the go
Nanoparticle dyes
boost storage
Briefs:
Fiber optics goes nano
Melted fibers
make nano channels
Wet biochip preserves
proteins
Nanotubes grown on
plastic
Hardy molecule makes
memory
Atoms make quantum
coprocessor
News:
Research News Roundup
Research Watch blog
Features:
View from the High Ground Q&A
How It Works
RSS Feeds:
News | Blog
| Books 
Ad links:
Buy an ad link
Advertisements:
|
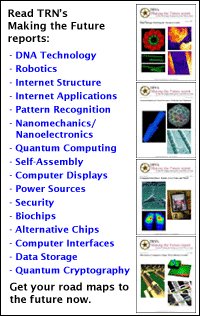
|
|
|