Virtual
view helps run tiny factory
By
Chhavi Sachdev,
Technology Research News
Constructing a machine from parts smaller
than the human eye can see is one of the biggest challenges in micromachinery.
Precision is difficult because the machines assembling the parts are huge
in comparison with the products they fabricate. Because the work space
is so cramped, small movements must be precise so that the tools do not
collide, and the force applied by the tools must be well-controlled so
parts are not crushed.
In addition, because the whole process is so small, it is difficult to
see that tasks are being performed correctly.
To address these problems, a team of researchers in France and Japan has
designed a desktop microfactory that allows a person to set up microassembly
processes by walking through a virtual assembly line.
The system provides a human operator with a virtual, three-dimensional
map of the scene, said Antoine Ferreira, an associate professor at the
Vision and Robotics Laboratory of Bourges in France. The virtual interface
is a simulation of the microworld that represents all the tasks of microfactory
processing.
In the planning stage, the operator configures the positioning, measurement,
handling and movement of all the different parts by using the interface
to verify the feasibility of semi-automatic tasks such as assembling the
gears of a watch. The tasks can then be carried out in a continuous cycle.
The simulation allows the operator to estimate the accuracy, cycle time,
and physical limits of the automated assembly of microelectromechanical
systems (MEMS) before they are implemented in a microfactory
The human operator, as in a macroscopic factory, “is a supervisor controlling
the…on-line execution of the assembly tasks through the VR interface,”
said Ferreira. If an object were damaged, or a microtool broken, the operator
could switch to manual mode to fix it, he said.
Using the microfactory simulation to plan ahead speeds up the microassembly
process and makes it more efficient, said Ferreira. "In terms of reduction
of execution time, lost energy, reduction costs, [and] precision of the
assembled parts, there is a reduction factor ranging from 10 to 50," Ferreira
said.
Research in this area has been ongoing for quite a while but the simulations
are not suitable for practical use yet, said Yu-Chong Tai, an associate
professor of electrical engineering at The California Institute of Technology.
“Demoed micro-machine tools by Japan are far from being satisfactory in
terms of performance. Big machine tools are still better in terms of accuracy
and ease of use,” he said.
The microfactory system would be used "for fast micro-prototyping,
but this will not be real for industry for many years to come," Tai
said.
The system is clearly feasible, said Russell Taylor, a research associate
professor of computer science, physics and astronomy, and materials science
at the University of North Carolina at Chapel Hill.
The researchers' contribution to the field "is in their closed loop
position/force feedback system that moves objects from one location and
orientation to another," Taylor said. "Their system is not what
I would call VR [since] it is not immersive, but standard through-the-window,
two-dimensional computer graphics," he said.
Several different kinds of virtually-assisted microsystems could be in
use within the next five years, Ferreira said. The simulation could be
used to assemble products like watches, very small circuit board components,
and microprocessors. It could also be used to manufacture microsensors,
cellular phone parts, and eventually even microrobots and micromachines,
he said.
The researchers' next step is to improve the system’s accuracy. The current
system is accurate to within three microns. They are also aiming to join
together the processes that they have demonstrated separately. Watches,
for example, are assembled from several dozen hybrid parts. The researchers
are aiming for an automated microfactory that handles, conveys, manipulates,
and assembles all the different micro-sized objects in one process.
Ferreira's colleagues were Jean-Guy Fontaine at the Vision and Robotics
laboratory at the University of Orléans, France, and Shigeoki Hirai at
the Micro-Robotics Lab of the Electrotechnical Laboratory, in Tsukuba,
Japan. The research was funded by the Japanese National MITI Micromachine
project, and the Higher Engineering School of Bourges. The research was
presented at the 32nd International Symposium on Robotics, April 19-21,
2001 in Seoul, Korea.
Timeline: > 5 years
Funding: government; University
TRN Categories: Microelectromechanical Systems (MEMS);
Robotics; Data Representation and Simulation
Story Type: News
Related Elements: Technical paper, "Visually servoed force
and position feedback for teleoperated Microassembly based virtual reality,"
proceedings of the 32nd International Symposium on Robotics, April 19-21,
2001, Seoul, Korea.
Advertisements:
|
July
18, 2001
Page
One
HP maps molecular memory
Cartoons loosen
up computer interfaces
Virtual view helps
run tiny factory
Bioengineers
aim to harness bacterial motion
Lasers spin electrons
into motion
News:
Research News Roundup
Research Watch blog
Features:
View from the High Ground Q&A
How It Works
RSS Feeds:
News | Blog
| Books 
Ad links:
Buy an ad link
Advertisements:
|
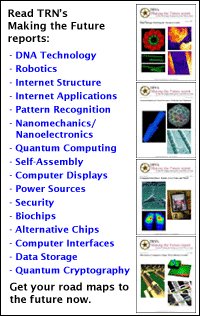
|
|
|