Plastic
process produces puny pores
By
Kimberly Patch,
Technology Research News
The size of the microscopic pores in a
material determines how the material scatters the sun's rays and how much
light will shine through. Making microscopic pores precisely the right
size, however, is tricky.
Researchers from the Massachusetts Institute of Technology have found
a way to coat materials with layers of polymer that allows them to control
the size of the polymer's microscopic pores.
The method has several key attributes. The water-based process is inexpensive
and can be used to coat delicate materials like the plastic used for sunglasses.
Exposing the coating to a water solution of a certain acidity also changes
the size of the pores even after they are in place. "When we change the
pH of a water solution we can fill [the polymer layers] with air [forcing]
them to become porous materials," said Michael Rubner, a professor of
materials science and engineering at the Massachusetts Institute of Technology.
Pore size that changes depending on pH could eventually prove useful for
biological applications like delivering drugs to specific areas within
the body, according to Rubner.
The researchers have also found ways to pattern layers of the polymers
on surfaces. "These are all water-soluble polymers [so] we can put water
into an inkjet printer at the right pH and wherever the ink goes the polymers
dissolve," said Rubner. This could lead to patterned surfaces that direct
cell growth.
Controlling the size of pores means controlling the amount of air the
coating contains, and thus the amount of glare that bounces off a material.
"Air has the lowest refractive index you can have. So the more air you
put into a material, the lower its refractive index is," said Rubner.
The refractive index of a material determines how much light it reflects.
"If you pass light through a sheet of glass, at each surface you'll lose
four percent of that light -- it's reflected," said Rubner.
Getting rid of glare means giving a material a top layer that has a refractive
index that's lower than the refractive index of a material. The thickness
of the coating also matters.
The right combination of refractive index and thickness will cause the
waves to cancel each other out and the light to pass through the glass,
said Rubner. "For example, if I took a beam of 100 percent intensity and
measured it after it passed through [plain] glass it would be down to
92 percent," he said.
Glass with reflective coatings, however would cause disruptive interference
so that "light that normally would be reflecting can't reflect anymore
so it has to go through the glass. Now you've got 99.9 percent of the
light you started off with coming out the other end rather than 92 percent,"
he said.
There's a caveat, however. This will tune out light waves of a certain
wavelength over only a 10-nanometer range. "If you go to different wavelengths,
you don't have the same kind of effectiveness," said Rubner. Visible light
waves vary from 400 to 700 nanometers, and the sun's rays extend even
further.
The way to broaden the antireflection capabilities is to grade the refractive
index. This is commonly done in the natural world: a moth eye achieves
this with a group of cones on the surface of the cornea, said Rubner.
"Think of it as a bunch of mountains sitting on the surface of the cornea,"
he said. At the very top of the mountains there is a small amount of mountain
and a lot of air, and the ratio changes all the way down, and near the
bottom the ratio is reversed. "If you create a graded refractive index...
you can broaden [the range of light waves] to hundreds of nanometers."
The researchers were able to make anti-reflective coating from their polymers
by making very small pores. This was a challenge, said Rubner. "Just recently
we figured out... that by applying some subtle games with the solutions
that... convert [the polymers] from the nonporous to the porous state
[we could] make the pores very very small," he said.
The researchers can now control the size of the pores from one micron,
which is large enough that the material scatters light, down to a tenth
of a micron, where it has anti-reflective properties, said Rubner.
To make the coatings, the researchers dip a glass or plastic substrate
into a solution of water mixed with the polymer, a long, chain-like, molecule
that can contain a negative or positive charge. "These polymer molecules
will spontaneously... assemble on the surface into a very, very thin layer,"
said Rubner. Once a layer builds up, its charge repels any more polymer
from attaching.
The researchers add another layer by putting the substrate in a negatively-charged
vat of polymer solution. "The negatively-charge polymer is attracted to
the positively-charge polymer. It neutralizes that charge and builds up
a little excess charge," said Ruben. The excess charge repels further
negatively-charged polymer.
The researchers can adjust the thickness of each layer from about half
a nanometer to about 50 nanometers per layer. "The thinnest film that
we put down is basically the thickness of the molecule itself," said Rubner.
The thickness of a layer depends the number of charges contained in the
polymers that make up the layer. "If you have a lot of charge on the chain
[it will] spread out on the surface," said Rubner. "If you put a few charges
on the chain, a few charges will anchor, but the rest of the chain will
loop away from the surface, so you end up getting a much thicker layer."
To make a 100-nanometer-thick film, which would have anti-reflection properties
for visible light, the researchers could build up, for example, 10 layers
that were 10 nanometers thick. "We do a fair amount of dipping... until
we get precisely the thickness we want," said Rubner.
To change the size of the pores, the researchers change the number of
charges on the negative polymer layers by dipping the substrate in liquid
somewhere between a pH of seven and two. When it comes in contact with
a high pH, a negatively-charged polymer is fully charged, and with a low
pH it is only partially charged. As the pH rises, the molecules release
hydrogen protons, which are positively charged. This increases the number
of negative charges on the chain, which causes the molecule to flatten.
The film can change its thickness by as much as a factor of three this
way, Rubner said. "You're filling it with air," he said.
For anti-reflective applications, the pore size can be permanently fixed.
Once the layers reach a desired thickness, they can be set by baking them
at a temperature of 60-90 degrees Celsius, said Rubner. "Once you have
the conditions you want -- the right velocity, the right thickness --
we [heat it] up in the oven at a relatively low temperature and we chemically
fix the structure so it can never change again."
The researchers are currently working on improving the adhesion of layers
on different substrates. At the same time they're looking to use the controllable
pore sizes in biological applications. "You could change what is passing
through a filter, for example, or you could have a drug inside a [controllable]
multilayer and then open the pore and release it," said Rubner.
Something like a change in pH could open the pores, and it's well known
that tumors in the human body create a different pH locally around them
than the body normally has, said Rubner. "It's speculative, and we have
no evidence to prove that we can do that yet, but it's potentially possible
[to] direct some of these materials to tumors and have them release a
drug," he said.
The other potential biological applications include culturing cells. "You
want to control where those cells are anchored, and what nutrients are
feeding them," said Rubner. To do this "you need to have patterned surfaces
to control where the cells attach and how they interact with the substrate
[that] they're sticking to."
The method is ready to use in making anti-reflection coatings now, said
Rubner. All that's needed is to "identify the application, look at the
substrate that you want to put [the coating] on, and... make sure that
[it] adheres well and it doesn't rub off easily," he said.
Using the coatings for uses like drug delivery is probably five years
away, he said.
Rubner's research colleagues were Jeri'Ann Hiller and Jonas D. Mendelsohn.
They published the research in the September, 2002 issue of the journal
Nature Materials. The research was funded by the National Science Foundation
(NSF).
Timeline: Now, 5 years
Funding: Government
TRN Categories: Chemistry; Materials Science and Engineering
Story Type: News
Related Elements: Technical paper, "Reversibly Erasable
Nanoporous Anti-Reflection Coatings from Polyelectrolyte Multilayers,"
Nature Materials, September, 2002.
Advertisements:
|
January
15/22, 2003
Page
One
Heat's on silicon
Remote monitoring
aids data access
Metal stores more hydrogen
Device demos terabit
storage
Plastic process
produces puny pores
News:
Research News Roundup
Research Watch blog
Features:
View from the High Ground Q&A
How It Works
RSS Feeds:
News | Blog
| Books 
Ad links:
Buy an ad link
Advertisements:
|
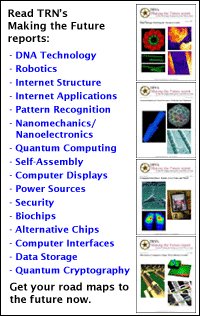
|
|
|