Electricity shapes nano plastic
By
Kimberly Patch,
Technology Research News
Researchers from the University of Groningen in the Netherlands and the University of Massachusetts at Amherst have found ways to use electricity to coax microscopic amounts of plastic to form patterns containing columns and tubes.
The microscopic plastic features are as small as 100 nanometers, which is 50 times smaller than a red blood cell, and could be used to make electronic and mechanical devices at that scale. "The structures can be fairly complicated and we have a wide range of different patterns," said Ullrich Steiner, a professor of polymer physics at the University of Groningen.
The method could be used for plastic electronics, light-emitting diodes, solar energy devices, and optical filters, according to Steiner.
Key to the method was a simple discovery: different plastics react to an electric field at distinctly different rates, making one plastic melt before another. The researchers were able to use this interplay between two types of plastic to make smaller features.
These sequential effects were a bit of a surprise, said Steiner. "I initially expected a much more complex interplay," of the two types of plastic, he said.
To make the tiny plastic forms, the researchers spread a thin layer of plastic film onto a silicon wafer, added a second silicon wafer in such a way that a layer of air remained, then attached electrodes spaced less than one thousandth of a millimeter apart.
They put between 30 and 70 volts of electricity through the electrodes. "The spacing between the electrodes is very small -- this translates to extremely high electric fields," Steiner said.
The fields are strong enough to heat the device and liquefy the plastic. When this happens, "the polymer-air double layer tries to align its interface parallel to the electric field lines," said Steiner. This generates tiny plastic columns that span the two plates.
The researchers made hollow tubes by adding a second layer of plastic to the sandwich. In this arrangement, the interface between the top layer of plastic and the air layer changed much more rapidly than the interface between the two types of plastics, said Steiner.
The top plastic layer formed columns that spanned from the surface of the second polymer layer to the top silicon wafer. After these columns were formed the second plastic layer liquefied and was drawn upward on the outside of the original columns. "This leads to... columns of polymer one that are coaxially coated with polymer two," said Steiner. The second polymer made a thin layer on the outside of these columns, similar to bark covering the trunk of a tree, he said. "The width of the bark is much smaller than the width of the entire tree trunk," he added.
The researchers then removed the initial columns to leave tiny plastic cylinders. The wall thickness of this second polymer structure -- the bark -- can be much smaller than the original column diameter, he said.
The researchers were able to adjust the diameter by changing how long they allowed the process to go on and by changing the thickness of the bottom layer of plastic, said Steiner.
The method can also be used to make patterns. If the silicon plate contains a pattern, the pattern changes the electrical field, which, in turn, changes the plastic formation. "The polymer is drawn towards the region of highest electrical field -- toward the regions where the topographic protrusion of the top plate extends downward," said Steiner. "This leads to replication of the pattern of the top plate into the polymer film," he said.
A second layer of plastic could be made to form a slightly different pattern. "Since the electrostatic forces are a function of the local film thickness, these forces pull with a differing strength on the film surface depending on its... thickness, and therefore replicate the imposed pattern differently," he said.
The technique is fairly generic -- it can be carried out using nearly any type of plastic, other types of liquids, and many different top and bottom surfaces, said Steiner. It also fits well with existing lithography equipment like that used in computer chip manufacturing.
It is particularly appropriate for making plastic electronics, including light-emitting diodes and photovoltaic devices, said Steiner. "In these applications, the active layer typically contains more than one component. The ability to simultaneously pattern more than one polymer... may be beneficial for the performance of these devices," he said.
On the minus side, the plastic layer touches the silicon master pattern, and it is also important to keep dust away, said Steiner. "The preparation and superposition of the two films has to be without flaw, and dust is a major issue," he said.
Carrying out several lithographic steps in a row could also prove difficult, said Steiner. "Suppose we replicate first a line pattern, and then, in a second step we coat the sample again with a homogeneous polymer film, with the aim to reproduce a second line pattern superposed to the first one at 90° to generate a cross-hatched pattern," he said.
The second step is a challenge because "the coat's surface topography will to some extend mirror the first line pattern," said Steiner. The second layer will be more efficient at replicating the pattern at the junctions where lines cross, while other parts of the lines are likely to reproduce less well, he said.
The researchers haven't tested this aspect of the method thoroughly enough to know whether this will prove a real limitation, Steiner added.
The researchers are exploring ways to use the method to make self-cleaning surfaces and anti-reflection coatings, and ways to construct layers that will be super-conducting. They are also working on ways to construct photovoltaics, said Steiner. And they are looking into the influence of electrical fields on polymer bonds, and forces generated by differences in temperature in polymer films, he said.
The researchers are working with a company to commercialize the technique, said Steiner. "I hope to see an application [in] plus or minus five years," he said.
Steiner's research colleagues were Mihai D. Morariu and Nicoleta
E. Voicu from the University of Groningen, Erik Schäffer at the Max Planck
Institute in Germany, and Zhiqun Lin and Thomas P. Russell from the University
of Massachusetts at Amherst. They published the research in the December,
2002 issue of the journal Nature Materials. The research was funded
by the Dutch Science Foundation (NWO), the German Science Foundation (DFG),
the National Aeronautics and Space Administration (NASA) and the National
Science Foundation (NSF).
Timeline: 5 years
Funding: Government
TRN Categories: Materials Science and Engineering; Microfluidics and BioMEMS
Story Type: News
Related Elements: Technical paper, "Hierarchical Structure
Formation and Pattern Replication Induced by an Electric Field," Nature
Materials, December, 2002
Advertisements:
|
July 16/23, 2003
Page
One
Sensors guard privacy
Cheaper optics-chip
link on tap
Logic clicks with
ratchet
Electricity shapes
nano plastic
News briefs:
Experience handed
across Net
3D display goes vertical
Gel yields nanotube
plastic
Nano toolbox
gains carbon cones
Jolts mix micro fluids
Jet-laser tandem
prints gold
News:
Research News Roundup
Research Watch blog
Features:
View from the High Ground Q&A
How It Works
RSS Feeds:
News | Blog
| Books 
Ad links:
Buy an ad link
Advertisements:
|
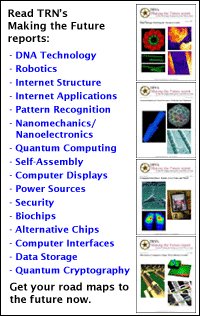
|
|
|