Microfluidics make flat screens
By Eric Smalley, Technology
Research News
As flat-panel
displays get bigger, the combination of complicated manufacturing equipment
like vacuum deposition chambers and the increased chances of defects, given
the larger screen areas, significantly boosts the cost of making the silicon
backplanes that power the screens.
Backplanes that use organic, or plastic, transistors have the potential
to be much easier and less expensive to produce. But existing methods of
making organic transistors, which include photolithography processes similar
to chipmaking techniques, screenprinting, and inkjet printing, have shortcomings
ranging from expense to imprecision.
Researchers from the Palo Alto Research Center have turned to a
technology used in biochips to overcome these problems. The researchers
are using microfluidic devices, which contain tiny channels that control
the flow of small amounts of fluids, to form organic transistors.
The process precisely aligns the polymer that makes up the bulk
of the transistor with metal electrodes, and further simplifies organic
manufacturing by allowing a semiconductor to be deposited and patterned
in a single step, said Michael Chabinyc, a research scientist at the Palo
Alto Research Center.
The polymeric thin film transistors could lead to inexpensive large-area
flat-panel computer displays. The flexible transistors could also make foldable
electronic paper backplanes possible.
The researchers made an organic backplane prototype by printing
a pattern of wax on a metal-coated transparent surface to define an array
of circuits, then chemically removing metal left uncovered by the wax. They
coated the surface with a photocurable polymer and shined ultraviolet light
from the bottom to cure the polymer. The metal circuits blocked the light,
which left the polymer above the circuits uncured. They washed away the
uncured polymer to make channels directly aligned above the circuits. Once
this mold was made, the researchers formed transistors by depositing liquid
polymer semiconductor material into the channels and letting it dry in place.
Key to the simplicity of the manufacturing process is that it uses
a passive fluid control process. Putting the liquid polymer semiconductor
in place required no force because "the microfluidic channels act as a wick
to draw the solution containing the polymer semiconductor across the array,"
said Chabinyc.
The researchers made microchannels that were 40 microns wide and
20 microns high. The pixel areas were 300 microns across. A micron is one-thousandth
of a millimeter.
The performance of transistors made using the process is comparable
to organic thin-film transistors made using existing methods, said Chabinyc.
But the process is simpler than other techniques, he said.
The method does not require semiconductor materials that are engineered
to handle the harsh conditions of the photolithography processes used to
make thin film transistors, according to Chabinyc. It can also produce smaller
structures than those made by screenprinting, and avoids the problem of
controlling the spread of inkjet droplets, according to Chabinyc.
The researchers' approach also avoids vacuum processing. Small-molecule
organic semiconductors are usually deposited onto a backplane surface using
vacuum coating techniques to make thin-film transistors. Because the researchers
use a polymer semiconductor that can be dissolved in a solvent, "the method...
can be done in the ambient environment; thus the commercialization of the
process should be less expensive," said Chabinyc. The process can be used
to pattern any semiconductor material that can be dissolved, he said.
Using a microfluidic process to form electronics is not a new concept.
Researchers have used patterned rubber stamps pressed against surfaces as
molds to make circuits. But the stamp method has its drawbacks, including
air bubbles, the difficulty of aligning the stamp with features on the surface,
and the difficulty of filling the channels without depositing excess material
on the surface, according to Chabinyc.
Polymer thin film transistors could be used in large-area displays
and electronic paper in five to ten years, said Chabinyc. "There's much
work to be done to improve the lifetime and environmental stability of organic
devices before they can be commercialized," he said.
Chabinyc's research colleagues were W. S. Wong, K. E. Paul and Robert
Street. The work appeared in the November 17, 2003 issue of Advanced
Materials. The research was funded by the National Institute of Standards
and Technology. The researchers also received samples from Dow Chemical
Company and Xerox Research Center of Canada.
Timeline: 2 years
Funding: Government
TRN Categories: Integrated Circuits; Materials Science and
Engineering; Microfluidics and BioMEMS
Story Type: News
Related Elements: Technical paper, "Fabrication of Arrays
of Organic Polymer Thin-Film Transistors Using Self-Aligned Microfluidic
Channels," Advanced Materials, November 17, 2003
Advertisements:
|
December 17/24,
2003
Page One
PDA translates speech
Device guards Net
against viruses
Body handles nanofiber
Microfluidics make
flat screens
Briefs:
Chemists grow nano
menagerie
Solid fuel cell
works in heat
Hybrid crypto secures
images
Chip uses oil
to move droplets
Light spots sort
particles
Organic transistors
get small
News:
Research News Roundup
Research Watch blog
Features:
View from the High Ground
Q&A
How It Works
RSS Feeds:
News | Blog
| Books 
Ad links:
Buy an ad link
Advertisements:
|
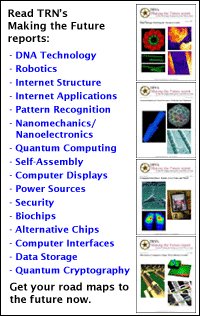
|
|
|