Fibers mix light and electricity
By
Kimberly Patch,
Technology Research News
Information
technology relies heavily on two very different types of manufacturing processes:
microtechnology and fiber optics.
Microtechnology manufacturing plants make devices by precisely combining
metal, insulator and semiconducting materials using complicated equipment
under clean-room conditions. The devices can contain many microscopic components,
making it possible to form intricate devices like computers on a single
chip.
Optical fiber plants draw large blocks, or preforms, of glass or
plastic into long, thin fibers. Compared to making microtechnology devices,
drawing fiber is relatively simple. Fiber-optic lines are made from one
or a few materials, often drawn so the fiber has a hollow core. The trick
to drawing fiber, however, is making sure materials are compatible enough
to be drawn together to form a thin fiber that maintains the ratio and positioning
of the materials in the preform.
Many researchers are making tiny circuits that channel light. Scientists
from the Massachusetts Institute of Technology have gone in the other direction
by demonstrating that it is possible to make some semiconductor devices
in optical fiber form.
Ordinary optical fiber carries photons within a hollow core; the
photons are confined to the core by the mirror-like glass or plastic fiber.
The researchers took the concept a step further by adding metallic wires
that conduct electricity to make a fiber photodetector. When light hits
the fiber, it causes a change in the electrical conductance of the wire.
They then took another step to make a more complicated photodetector that
senses specific wavelengths.
"We are trying to establish [that] fiber can now be thought of as
an integrated device -- it has some electronic functionality, it has optical
filtering," said Yoel Fink, an assistant professor at the Massachusetts
Institute of Technology.
The method could eventually be used to make very inexpensive, large-area
electronic devices including screen-like light detectors that could sense
changes in light or heat. Such a detector could eventually serve as a security
fence, a sensor for a car, or an interface between a computer and a laser
pointer, said Fink.
The researchers' prototype photodetector fiber has four layers.
From the outside in, these are a thermoplastic polymer, a glass/polymer
mix that forms a filter, and four tin electrodes surrounding a semiconducting
glass inner core that channels light.
The fiber is flexible but also durable, making it possible to weave
it into other materials.
The key to making a more complicated device in a fiber was finding
ways to draw the right types of materials together, said Fink. Conventional
wisdom says you can only draw materials that are similar in all their properties,
said Fink. "People thought that they could just draw silica, maybe silica
with holes, or just polymers," he said. The argument was that the structures
would break apart if the materials did not have similar thermomechanical
properties like viscosity.
The researchers found that they had more latitude in putting materials
together than previously thought. They demonstrated that it is possible
to draw materials together that have similar but not exact melting, or glass,
transition temperatures, and similar viscosity.
The keys to forming proper layers were engineering the viscosity
of the materials and the shape of the preform elements, and drawing the
material at high tension to cut down on the negative effects of surface
tension, said Fink. One of the materials in the researchers' fiber photodetector
is a glass that contains tin to increase its viscosity, said Fink.
"Behind this is a study of surface energy between the various elements
which is something we measure very carefully at the temperature of the draw,"
said Fink. The correct mix makes it possible to draw several different materials
together without them breaking up, he said.
Devices made from fiber have several pluses, said Fink. The devices
can be made very long, nearly transparent, can cover large areas, and are
flexible enough to be woven into fabric. In addition, fibers can be made
very cheaply. "The entry-level -- the price you need to pay in order to
[make devices from fibers] is far, far lower than anything associated with
semiconductors," said Fink. "It is many orders of magnitude lower."
The researchers' photodetector senses light anywhere along its length,
and a screen of 100 by 100 photodetector fibers woven together could pinpoint
the location of light shining on it. A similar device made from traditional
electronics would be much more expensive because it would need 10,000 traditional
photodetectors, said Fink.
Such screens could be used as security fences, said Fink. Today's
security fences contain pressure sensors that indicate if a person climbs
on it. Photodetector fibers embedded in a security fence would be able to
sense heat or a change in backlighting when a person got close to the fence,
he said.
A photodetecting fiber screen could also be used as a large computer
input device controlled by a laser pointer.
The fibers could also be embedded in the windshield of a car to sense
where a driver is looking, said Fink.
A security-fence application that has to do with identifying a point
of illumination could be practical within two years, said Fink. Driver-sensor
and light-based computer interfaces made from the fiber could become practical
in three or four years, he said.
The researchers are working on more complicated fiber devices, said
Fink. "Photodetection is a very close relative of [light] emission and a
very close relative of the transistor," he said. "[We are] trying to expand
the functionality in a single fiber so we can get a transistor."
Ultimately, if the researchers can engineer the electronic properties
of the fibers in a fine enough manner, they could create many types of electronic
devices in fiber form, said Fink.
Fink's research colleagues were Mehmet Bayindir, Fabien Sorin, Ayman
F. Abouraddy, Jeff Viens, Shandon D. Hart and John D. Joannopoulos. The
work appeared in the October 14, 2004 issue of Nature. The research
was funded by the Defense Advanced Research Projects Agency (DARPA), the
Army Research Office (ARO), the Office of Naval Research (ONR), the Air
Force Office of Scientific Research (AFOSR).
Timeline: 1-2 years, 3-4 years
Funding: Government
TRN Categories: Optical; Materials
Story Type: News
Related Elements: Technical paper, "Metal-Insulator-Semicconductor
Optoelectronic Fibres," Nature, October 14, 2004
Advertisements:
|
November 17/24, 2004
Page
One
Fibers mix light
and electricity
Software sorts out
subjectivity
Nanomechanical memory
demoed
Nanotubes tune in light
Briefs:
Low-pressure
material holds hydrogen
Plastic cuts
artificial hip wear
2D holograms
make 3D color display
Lasers drive nano
locomotive
Light-recording
plastic holds up
Atom flip energy measured
News:
Research News Roundup
Research Watch blog
Features:
View from the High Ground Q&A
How It Works
RSS Feeds:
News | Blog
| Books 
Ad links:
Buy an ad link
Advertisements:
|
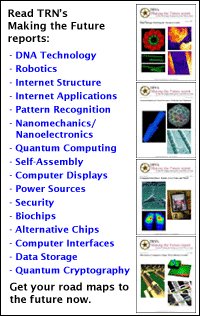
|
|
|