Wires make wireless strain gauge
By
Ted Smalley Bowen,
Technology Research News
Buildings may seem to embody inertia, but
in reality they bristle with all manner of tension and compression --
dead loads like interior walls, live loads like people and furniture,
and locked-in loads like those in pre-stressed concrete.
Then there are dynamic forces -- everything from the drop of a
shoe to high winds and earthquakes. The effects of these forces can be
difficult to predict and to detect. For example, even when a quake fails
to bring a building down, there can be extensive damage, some of it invisible
to the naked eye.
In recent years, designers have incorporated increasingly sophisticated
mechanisms for dampening and countering violent shifts. Seismic retrofits
and new construction place buildings on rollers and put dampers on joints
and walls.
And embedded sensors in key places within walls, frames and foundations
allow designers, building managers, and inspectors to measure the conditions
that cause a building to topple, or gauge the soundness of a standing
structure that's been subjected to strong forces but does not bear visible
signs of strain.
Today's sensors measure forces like peak strain, peak displacement,
peak acceleration, story drift, absorbed energy and accumulated plastic
deformation, but can be expensive and difficult to read.
Researchers at Keio University in Japan have developed peak strain
and displacement building sensors that do not require a constant power
source, and that can be read using a wireless device. The sensors are
designed to be embedded in concrete and fire-protection coatings.
Peak strain and displacement are measures of maximum distortion
and shifting. Peak acceleration is the swiftest portion of distortion,
story drift measures the side to side displacement of a given story of
a building, absorbed energy is one measure of a jolt to a structure and
accumulated plastic deformation is the cumulative warping of a structure.
A strain sensor must change when it is subjected to stress and
must provide some way to read the change. Changes in electrical properties
like resistance, capacitance and inductance can indicate that a sensor
has undergone strain.
Resistance is a measure of how easily electricity flows through
a material. Capacitance is the amount of electric charge a material can
briefly store. Inductance is a measure of the voltage that can be induced
through a circuit when a magnetic field produces an electric charge in
a material.
The Keio design uses thin aluminum wires that stretch and remain
elongated when subjected to strain. The stretching changes the resistance,
capacitance and inductance of the wires, which can be measured relatively
easily. And because the change to the sensor is mechanical, the device
does not have to be powered. The researchers' design measures capacitance.
"Capacitance is our preference [because] the system is simple and cheap,"
said Akira Mita, a researcher at Keio University. Such sensors can be
made of any conductive material, he said.
Today's common embedded strain sensor designs work differently.
Some measure peak strain with transformation-induced plasticity (TRIP)
steel wires, which become magnetized when subjected to significant strains.
This type of sensor can only be used once, however, and measuring its
magnetism is relatively complicated.
Other embedded sensors are made from plastics reinforced with
carbon and glass fiber, but the sensors record both peak and residual
strains and untangling the two is difficult.
Two other approaches use carbon powder or shape-memory alloys
in place of carbon fiber, but these have drawbacks as well. Carbon powder
sensors are difficult to read and shape memory alloy sensors are tricky
to design.
The Keio researchers have made several versions of their sensor.
In one configuration, a thin wire is attached at one end to a block of
conductive material and sandwiched between layers of conductive material
at the other end. When pulled, the wire stretches, changing its electrical
resistance.
An alternate design uses a variable capacitor, variable inductor
or variable resistance element. Under strain, the wire in this scheme
does not change length, but the variable element records the strain.
The variable capacitor version was made of a pair of aluminum
cylinders separated by a nonconductive material and a 0.22-millimeter-thick
fluorocarbon wire.
The researchers added an inductor or capacitor, depending on the
sensor's design, that made it possible to sense the state of the wires
using a wireless receiver. The addition created a closed circuit, and
a change in the circuit's frequency indicated the change in capacitance
or inductance and thus the level of stress encountered.
The test data transmitted from the variable capacitor sensor compared
well with laser sensor readings of the same peak strain, according to
Mita.
The researchers also tested a variable resistor design consisting
of two potentiometers, thin wires, pulleys, a spindle and a spring. Potentiometers
indicate displacements side-to-side. The researchers device was able to
measure side-to-side shifts of up to 300 millimeters in each direction.
The next step is to make a version of the sensor that will record
several types of strain at once. The design has the potential to produce
sensors that read strain, stress, acceleration, cumulative displacement
and integrated displacement, Mita said. Integrated displacement measures,
which take into consideration multiple displacements, are used to estimate
the durability of an element.
The sensors are currently in use.
Mita's research colleague was Shinpei Takhira. The work was published
in the Feb. 17, 2003 issue of Smart Materials. The research was funded
by the Japan Iron and Steel Federation.
Timeline: Now
Funding: Corporate
TRN Categories: Materials
Story Type: News
Related Elements: Technical paper, "A smart sensor using
a mechanical memory for structural health monitoring of a damage-controlled
building," Smart Materials and Structures, Feb. 17, 2003
Advertisements:
|
June 18/25, 2003
Page
One
Chip sorts colors
Software referees group
calls
Prefab key to molecular
memory
Wires make wireless
strain gauge
News briefs:
See-through circuits
closer
Protein traps nanoparticles
Nods drive audio
interface
Nano rapid prototyping
advances
Practical nanotube
fiber near
Nanotube transistors
make memory
News:
Research News Roundup
Research Watch blog
Features:
View from the High Ground Q&A
How It Works
RSS Feeds:
News | Blog
| Books 
Ad links:
Buy an ad link
Advertisements:
|
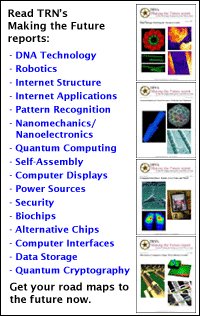
|
|
|