Photonic chips go 3D
By
Eric Smalley,
Technology Research News
The dream of building computer chips that
use light signals rather than electricity has entered the realm of serious
research in recent years with the advent of photonic crystal, a material
that blocks and channels light within extremely small spaces.
Producing practical photonic crystal chips, however, includes
several challenges: making three-dimensional devices that emit light from
specific points, emit at the wavelengths used by today's optical telecommunications
equipment and can be manufactured using processes suited to mass production.
Research teams from the Massachusetts Institute of Technology
and from Kyoto University have made devices that meet all three challenges.
The techniques could be used to make smaller, more efficient communications
devices; create optical memory and quantum computing and communications
devices; develop new types of lasers and biological and chemical sensors;
and could ultimately lead to all-optical computer processors.
The semiconductor industry took off with the advent of a practical
and low-cost method of integrating a large number of transistors into
a single chip, said Minghao Qi, a research assistant at MIT. "It is natural
then to envision the possibility of integrated photonics, where information
is processed fully in the optical domain [at the high] bandwidth of photons,"
he said.
Photonic crystal is usually made from the same semiconductor materials
as computer chips using common chipmaking techniques like photolithography.
It contains regularly spaced gaps of air or other materials that form
boundaries within the crystal that refract, or bend, specific wavelengths
of light. Refraction is responsible for the illusion that a drinking straw
bends at the air-liquid boundary. Portions of the materials that do not
contain gaps channel light within the crystal and emit light from it.
The MIT photonic chip has seven layers that each contain two types
of two-dimensional photonic crystal. One type is an arrangement of rods
surrounded by air and the other type is solid material perforated with
air holes. The rod slab is positioned above the hole slab in each layer,
and the layers are offset to produce steps. The holes are about 500 nanometers
in diameter, or about one-tenth the size of a red blood cell. The material
blocks light at wavelengths of 1.3, 1.4 and 1.5 microns. Telecommunications
systems use near-infrared 1.3- and 1.55-micron wavelengths.
The researchers filled specific air holes and gaps between rods
during the manufacturing process to create solid areas, or defects, that
emit light. "A critical goal in photonic crystal [research] is the ability
to put arbitrary defects with precisely controlled shapes and sizes at
designed locations," said Qi.
The two types of two-dimensional photonic crystal in each layer
of the three-dimensional crystal also allow for polarization control,
said Qi. A light beam's electric field is ordinarily oriented in a plane
perpendicular to the beam. The electric field of polarized light is confined
to one direction within the plane. Controlling polarization is important
because transferring light signals from photonic crystal to optical fibers
requires matching the polarizations of the devices, he said.
The crystal is more efficient than previous three-dimensional
photonic crystals, and the seven layers can be formed in four processing
steps, said Qi.
The Kyoto University team has advanced its existing woodpile-structured
three-dimensional photonic crystal with a method to make solid areas in
specific locations and have shown that the material precisely controlled
light, said Susumu Noda, a professor of electronic science and engineering
at Kyoto University.
The woodpile photonic crystal consists of perpendicular layers
of semiconductor rods. The researchers' design calls for 200-nanometer-wide
rods spaced 700 nanometers center to center. The photonic crystal controls
1.55-micron light.
The researchers also sandwiched a light source inside their photonic
crystal, which is a step toward fully integrated optical devices, said
Noda.
The MIT process could be used to make practical telecommunications
devices and biological and chemical sensors in two to three years, said
Qi. High-quality devices that could be coupled to optical fiber could
take five years, he said. Simple all-optical computer chips could take
10 years to develop, he said.
Devices based on the Kyoto method could become practical in five
to ten years, said Susumu.
Qi's research colleagues were Elefterios Lidorikis, Peter Rakich,
Stephen Johnson, John Joannopoulos, Erich Ippen and Henry Smith. The work
appeared in the June 3, 2004 issue of Nature. The research was
funded by the National Science Foundation (NSF).
Susumu's research colleagues were Shinpei Ogawa, Masahiro Imada,
Susumu Yoshimoto and Makoto Okano. The work appeared in the June 3, 2004
issue of Sciencexpress. The research was funded by Core Research
for Evolution Science and Technology (CREST), Japan Science and Technology
Agency (JST), and the Ministry of Education, Culture, Sports, Science
and Technology (MEXT) of Japan.
Timeline: 2-3 years, 5 years, 7-8 years,
10 years
Funding: Government, Corporate
TRN Categories: Optical Computing, Optoelectronics and Photonics;
Materials Science and Engineering
Story Type: News
Related Elements: Technical paper, "Control of Light Emission
by 3D Photonic Crystals", Sciencexpress, June 3, 2004; technical paper,
"A Three-dimensional Optical Photonic Crystal with Design Point Defects,"
Nature, June 3, 2004
Advertisements:
|
July 28/August 4, 2004
Page
One
Photonic chips go 3D
Online popularity tracked
Summarizer gets the idea
Electric fields assemble
devices
Briefs:
Process prints
silicon on plastic
Tool automates
photomontage edits
Device promises
microwave surgery
Hologram makes
fast laser tweezer
Chemistry yields
DNA fossils
Particle
chains make quantum wires
News:
Research News Roundup
Research Watch blog
Features:
View from the High Ground Q&A
How It Works
RSS Feeds:
News | Blog
| Books 
Ad links:
Buy an ad link
Advertisements:
|
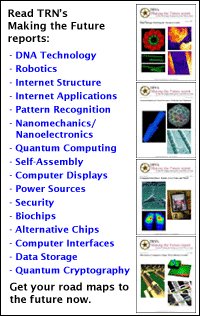
|
|
|